Sheet metal bending is a crucial aspect of metal fabrication that involves the deformation of a metal sheet into a specific shape or angle without removing any material. This technique is essential for creating a variety of components, such as brackets, enclosures, and frames, particularly using aluminum sheet metal.
The bending process applies force to the metal sheet, causing it to flex and take on the desired form. Knowledge of key factors like sheet thickness, bending angle, and the type of material being utilized is vital for both hobbyists and professionals engaged in bending sheet metal.
How Sheet Metal Bending Works
Sheet metal bending involves the manipulation of a metal sheet to achieve the desired shape. This process relies heavily on the principles of stress and strain, allowing the metal to undergo both elastic and plastic deformation. Understanding these concepts is crucial for successful metalworking, particularly when bending aluminum sheet metal, which requires unique considerations due to its lighter weight and malleability.
Bending metal sheet typically employs specialized tools to ensure accuracy and efficiency. One of the most common pieces of equipment used is the brake press. This machine applies a substantial amount of force to the sheet, enabling a precise bend. By calculating the correct bend radius, fabricators can prevent material failure, an important aspect of producing quality metal parts.
When discussing the bending process, the choice of dies is imperative. Different types of dies cater to various bending tasks, affecting the outcome significantly. Utilizing the right die enhances the effectiveness of the bending procedure and results in superior craftsmanship.
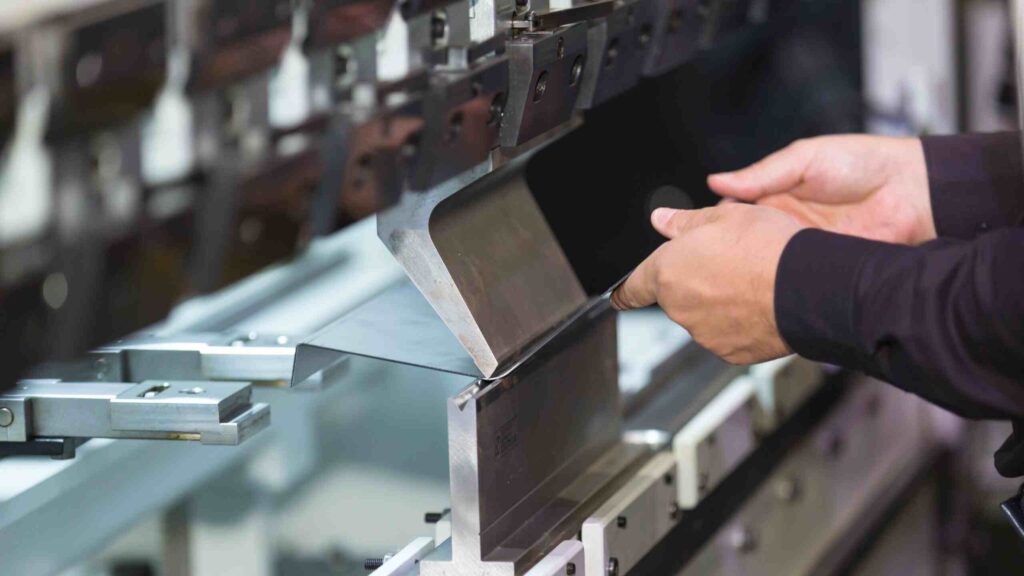
Different Types of Metal Bending
Understanding the different types of metal bending is essential in the field of sheet metal fabrication. Each technique serves unique purposes across various industries. Two primary methods dominate the landscape: cold bending and hot bending. These techniques differ significantly in their application and suitability based on the material involved.
Cold Bending vs. Hot Bending
Cold bending occurs at room temperature, making it suitable for most sheet metal applications. This method provides an excellent surface finish and precise dimensions, which are critical factors for many metal fabricators. Cold bending is often utilized in scenarios where rigidity and a polished appearance matter, such as in automotive parts and precision machinery.
On the other hand, hot bending requires the metal to be heated, which reduces hardness and enhances malleability. This technique allows for more complex shapes and forms. Metal fabricators typically use hot bending when dealing with thicker materials or when the design requires significant alteration of the metal’s structure. Industries such as construction and aerospace frequently apply hot bending for their heavy-duty components.
Feature | Cold Bending | Hot Bending |
---|---|---|
Temperature | Room Temperature | Heated |
Surface Finish | Excellent | Good |
Malleability | Lower | Higher |
Typical Applications | Automotive Parts, Precision Machinery | Construction, Aerospace |
Choosing between cold and hot bending depends on various factors, including the type of metal and the desired outcome. Both methods play a vital role in metal fabrication, catering to specific needs and industry standards.
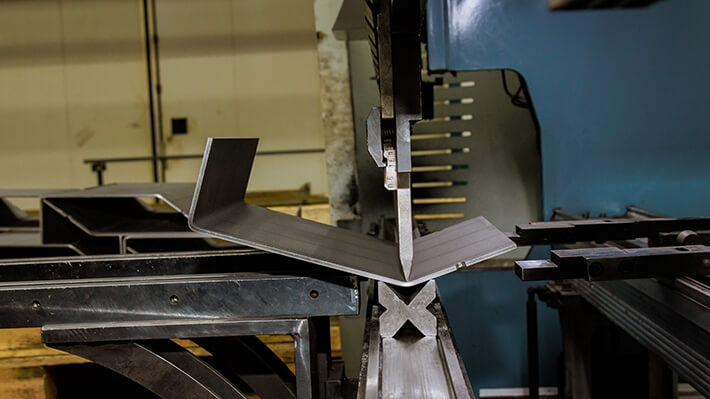
What Are Common Methods for Bending Sheet Metal?
Bending sheet metal involves various techniques, each serving specific purposes depending on the design and material requirements. Understanding the common methods for bending sheet metal can enhance the efficiency and precision of the processes involved. Among these methods are V-bending, U-bending, and edge bending, each with its unique advantages.
The Role of Tooling Techniques
V-bending is one of the most popular methods, known for its ability to create precise angles. This technique allows for versatility across a range of thicknesses, making it ideal for various applications. U-bending, on the other hand, is particularly effective for producing larger, curved components. This method excels in generating smooth bends while ensuring the integrity of the material.
Edge bending is crucial when a more pronounced bend is required, often utilized in components such as brackets or flanges. In this technique, the bending occurs at the edge of the material, allowing for tighter radii and optimized strength.
The choice of tooling plays a significant role in bending sheet metal. Select tools tailored for specific methods to achieve both efficiency and effectiveness in manufacturing processes. The right tooling not only improves the quality of the bends but also enhances the overall productivity in metalworking operations.
What Materials Are Good for Sheet Metal Bending Processes?
When considering materials for sheet metal bending, it’s essential to evaluate different types for their specific properties. Common choices include aluminum, steel, and copper, each bringing unique advantages to the bending process.
Aluminum, widely popular due to its lightweight nature and corrosion resistance, is ideal for bending applications. It excels in industries such as automotive and aerospace, making bending aluminum sheet metal a preferred choice for many manufacturers. Its malleability allows for intricate shapes and designs, ensuring versatility in projects.
Steel represents another significant material in metal bending, with stainless steel often leading the charge. Known for its strength and durability, stainless steel works well in demanding industrial applications. Additionally, it can withstand extreme environments, enhancing the quality of the bent products.
Copper, although less commonly used than aluminum or steel, provides excellent electrical conductivity. It is suitable for projects where conductivity is crucial, like electronic equipment enclosures. However, its cost could be a drawback in some applications.
Understanding how material thickness and grain direction affect the bending process is vital. Thicker sheets may require more force to bend, while considering the material grain ensures a smooth and effective bend without compromising integrity.
Material | Key Properties | Applications |
---|---|---|
Aluminum | Lightweight, corrosion-resistant, highly malleable | Aerospace, automotive, consumer products |
Stainless Steel | Strong, durable, resistant to rust and corrosion | Industrial applications, construction, food processing |
Copper | Excellent electrical conductivity, malleable but heavier | Electrical components, plumbing, roofing |
Benefits of Metal Bending
Bending metal sheets comes with a variety of advantages that enhance the efficiency of sheet metal fabrication. One significant benefit is cost-effectiveness. By employing bending techniques, manufacturers can minimize the need for additional processes like welding or extensive machining, leading to reduced labor and material costs.
The precision and repeatability offered by modern metal bending equipment further underscore the benefits of metal bending. Advanced machinery ensures that each bending metal sheet maintains consistent specifications, crucial for producing high-quality parts. This consistency is vital in industries that demand tight tolerances.
Versatility represents another major advantage. The ability to create intricate shapes allows for innovative designs and functional components across numerous applications. From construction materials to consumer electronics, bent metal can meet diverse needs effectively.
Lastly, the environmental aspect of metal bending cannot be overlooked. This process tends to create less waste compared to other methods of metal shaping. By optimizing the use of materials, manufacturers can contribute to sustainability efforts while reaping the economic rewards of efficient sheet metal fabrication.
Disadvantages of Metal Bending
Bending sheet metal presents several challenges that can impact both the quality and cost of a project. One of the primary disadvantages of metal bending is the risk of material fracture or deformation. If the bending process is not executed with precision, the material may not only bend as desired but could also crack or lose its intended shape altogether. This aspect requires careful attention during the design and execution phases.
Another significant limitation lies in the minimum bend radii. Depending on the type of material, there are specific thresholds that must be adhered to avoid compromising structural integrity. Exceeding these limits can result in subpar outcomes that affect overall product performance.
From an economic standpoint, high initial setup costs often serve as a deterrent for smaller fabricators. Investing in the right machinery and tools for bending sheet metal can be overwhelming, especially for startups or businesses with limited budgets. Additionally, the complexity of the bending process necessitates skilled labor. The need for specialized training can lead to further costs in hiring knowledgeable employees or providing existing workers with the necessary training.
Industries That Use Sheet Metal Bending
Sheet metal bending plays a crucial role in various sectors, demonstrating its versatility and importance in the world of metal fabrication. Different industries utilize this process to create essential components, underscoring the significance of skilled craftsmanship in these fields.
Applications in Various Sectors
The automotive sector heavily relies on sheet metal bending for manufacturing components such as chassis, body panels, and brackets. Aerospace industries utilize bending techniques to craft lightweight yet strong components like aircraft wings and fuselage structures. In the HVAC industry, ducting systems benefit from precise bends that ensure proper airflow and efficiency.
Construction is another prime area where sheet metal bending is essential. Architectural features, such as roofing systems and decorative elements, often utilize bent metal for both function and aesthetics. The trend towards customized metalwork is growing across these industries, as businesses seek unique solutions tailored to specific needs.
As the demand for specialized metal fabrication increases, so does the need for skilled metal fabricators. Their expertise in sheet metal bending helps manufacturers meet evolving standards and preferences, reinforcing the process’s relevance across multiple industries.
Tips for Bending Sheet Metal
Bending sheet metal can be a rewarding endeavor, but it requires precision and forethought. One of the essential tips for bending sheet metal is to take accurate measurements and plan your projects carefully. Ensuring that you have a clear understanding of dimensions and angles before you begin will help improve the overall outcome of your work, especially when dealing with delicate materials like bending aluminum sheet metal.
Selecting the appropriate tools is equally crucial. Tools tailored to your specific material can significantly enhance the bending process. For instance, using the right type of blade can ensure clean bends and reduce the risk of damage. Additionally, practicing on scrap material can provide valuable experience and help you hone your technique, making the transition to your final piece smoother.
Environmental conditions also play a significant role in achieving the best results. Maintaining proper blade alignment is vital, as misaligned blades can produce uneven bends. Remember also to prioritize safety; wearing protective gear is essential to secure your well-being while operating machinery. By implementing these best practices, you can amplify your success in bending sheet metal effectively and safely.