Metal laser cutting is a precise way to cut metals like aluminum and stainless steel. It uses high-powered laser beams. This technology helps manufacturers make detailed designs with great accuracy.
It’s key in metal fabrication. Metal laser cutting also has efficient processes. These processes give clean edges and cut down on waste.
Many companies offer laser cutting services. Send Cut Send and Online Metals are examples. They provide products like galvanized steel and aluminum sheet metal. They make sure customers are happy with their services.
How does Metal Laser Cutting Work?
The metal laser cutting process uses a focused laser beam on the metal. This creates intense heat, melting or vaporizing the metal. This results in clean and precise cuts.
Laser technology makes this process more efficient and accurate. It’s a key part of the cutting method.
Most systems use CNC machining. This allows them to follow detailed designs with automation. It helps manufacturers get consistent results, boosting productivity and precision.
Different lasers have different power levels for various needs. The gases used also impact the cut’s quality and speed. For example, oxygen works well with mild steel, while nitrogen is better for stainless steel.
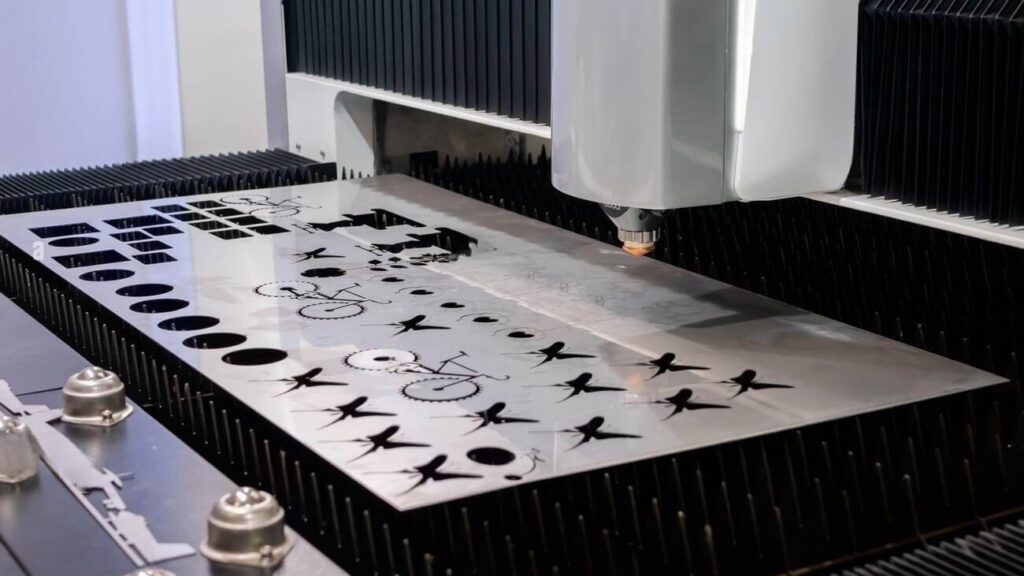
How to Laser Cut Metal
To laser cut metal well, start by picking the right metal sheet type and thickness for your project. Different metals need different cutting techniques. Then, make or find your design in a format that laser machines can use.
Next, set up your laser cutting machine correctly. Adjust settings like focus, power, and speed for the best results. Also, always wear safety goggles and keep the area free from flammable stuff.
If you want to try DIY laser cutting, many online guides can help. They’re great for both hobbyists and pros. They let you dive into creative metal cutting projects.
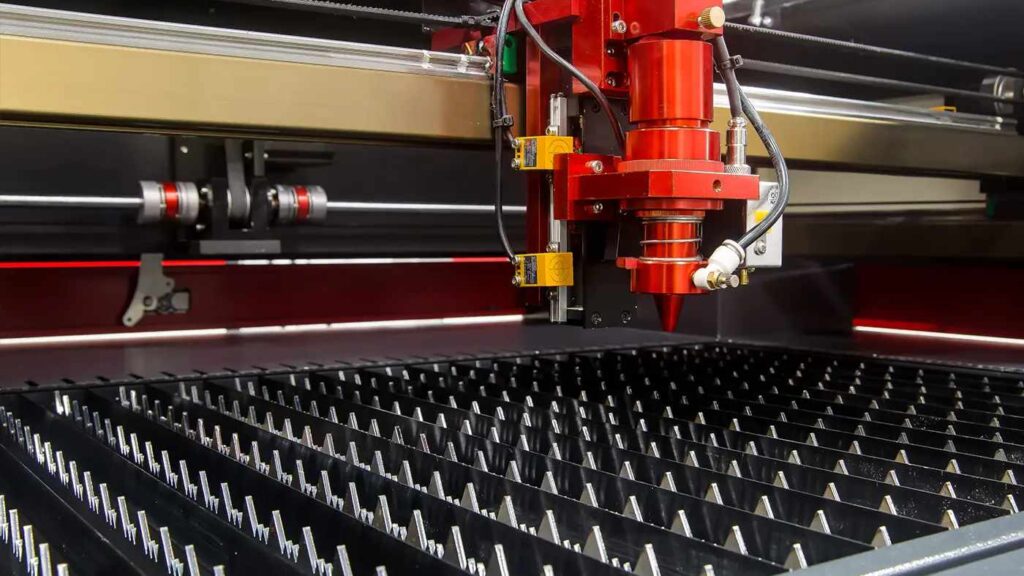
What Metal Material Can Be Laser Cut?
Laser cutting is great for cutting many metal types. This is key for lots of projects. Metals like stainless steel, aluminum, mild steel, copper, and brass work well with laser cutting.
Each metal has its own special traits. This affects how it’s cut and the settings needed. For example, stainless steel needs more power than aluminum. This means you have to adjust things to get the best results.
Many industries use metals like galvanized steel for roofs. They also use different metal sheets for building projects. Choosing the right metal is crucial for good cuts and quality products. Knowing what each metal is like helps makers get precise cuts. This makes laser cutting even better for projects.
What is the best laser for cutting metal?
Choosing the right laser for cutting metal means knowing about the different laser types. Fiber lasers and CO2 lasers are top choices. They work well for different metals and thicknesses.
Fiber lasers are very efficient and popular. They cut through tough metals like stainless steel and titanium fast and accurately. This makes them great for industries needing top-notch metal cutting. They also save money because they use less energy and need less upkeep.
CO2 lasers are better for thinner materials and non-metal substrates. They make precise cuts and are good for detailed designs. While they’re not as fast as fiber lasers on thick metals, they’re versatile and useful in many metalworking tasks.
When picking lasers, consider a few key things:
- Power output (measured in watts)
- Cutting speed
- Cut quality
Top brands like Amada and TRUMPF offer high-quality laser cutting machines. The right laser depends on your needs, like speed, material, or precision.
What are the main parameters of metal laser cutting process?
Understanding the key parameters of metal laser cutting is crucial for great results. Important factors include laser power, cutting speed, and the type of gas used. Each of these laser cutting parameters affects the quality, efficiency, and precision of the cut. It’s vital to consider them carefully.
What are the cutting tolerances for metal laser cutting?
Laser cutting is known for its high precision. The cutting tolerances depend on material type and thickness. They usually range from ±0.005 to ±0.015 inches. For complex shapes or thicker materials, tighter tolerances are needed, showing the importance of adjusting settings for each project.
What is the thickest metal that can be laser cut?
Advances in technology have increased the maximum metal thickness that can be laser cut. Today’s systems can cut steel up to 1 inch thick. Aluminum can be cut up to 0.5 inches thick. These advancements improve both efficiency and accuracy for thicker sections.
Material Type | Maximum Thickness | Typical Cutting Tolerance |
---|---|---|
Steel | 1 inch | ±0.005 to ±0.015 inches |
Aluminum | 0.5 inches | ±0.005 to ±0.015 inches |
What are the industries that utilize laser cutting for metal?
Laser cutting is used in many fields. In the automotive world, it’s key for making parts that fit together perfectly. This ensures cars are both high-quality and perform well.
The aerospace field also uses laser cutting. It helps make complex parts for planes, making them safer and more efficient. Shops use it for metal roofing and custom projects, creating designs that clients want.
Other areas like electronics, machinery, and construction also benefit. They need parts that meet strict standards. Laser cutting’s ability to make precise parts quickly is vital for today’s manufacturing. It boosts productivity and brings new ideas to the table.
Advantages and Disadvantages of Metal Laser Cutting
Metal laser cutting has many benefits that make it a top choice in manufacturing. It can make precise cuts with little waste, which is key for projects needing exact details. This technology can cut through many materials and thicknesses, making production faster and reducing wait times.
But, there are also downsides to consider. Buying high-quality laser cutting machines can cost a lot upfront. You also need to budget for ongoing maintenance. Additionally, the heat from cutting can warp some materials, so choosing the right materials and settings is important.
By looking at both the good and bad sides of metal laser cutting, companies can make better choices. Knowing the pros and cons helps manufacturers use this technology well. It also helps them stay ahead in the competitive market.
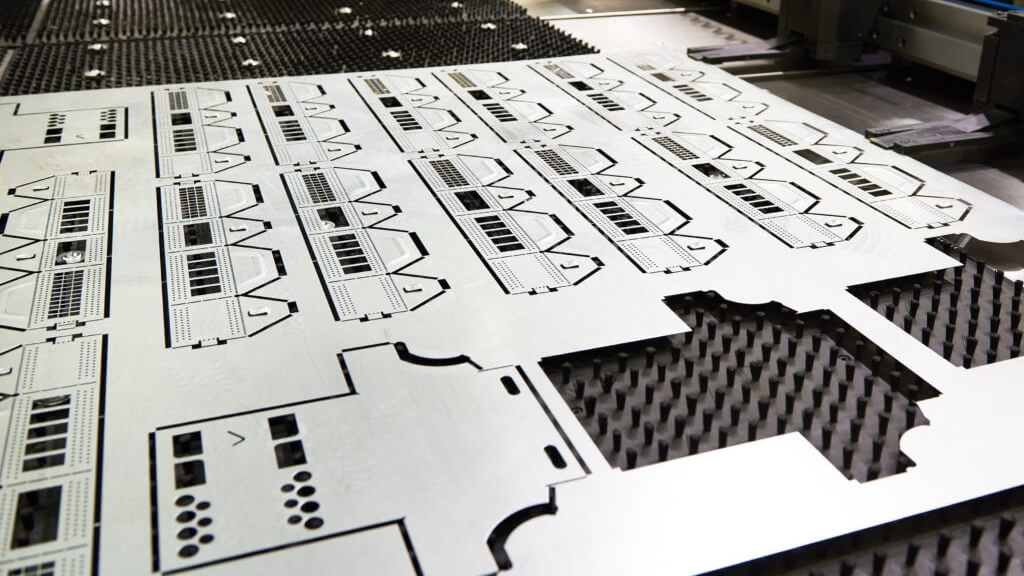