Bending
Sheet metal bending is a manufacturing process where force is applied to a piece of sheet metal to bend it at an angle and form the desired shape.
What Is Sheet Metal Bending?
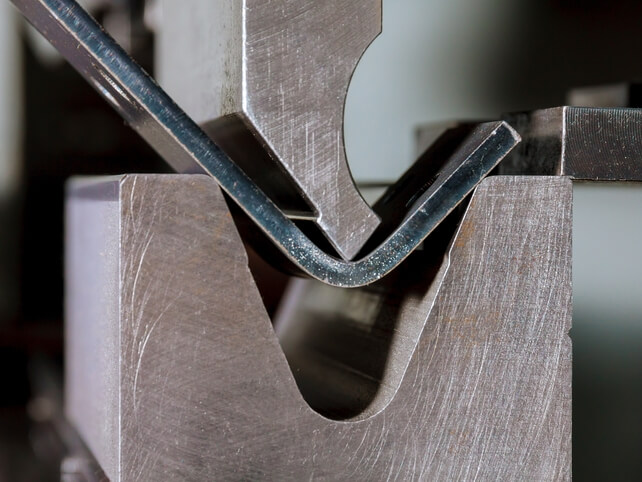
Sheet metal bending is a manufacturing process where force is applied to a sheet of metal to create a bend or angle, typically using tools like press brakes or folding machines. The process involves clamping the metal between a punch and die, then applying pressure to achieve the desired shape without compromising the material’s integrity. It is widely used to produce components like brackets, enclosures, and panels, offering high precision and repeatability. The method can handle various metals, including steel, aluminum, and copper, making it versatile for creating complex, functional parts.
The bending process can be customized to achieve different angles, radii, and shapes, depending on the design requirements. Techniques like air bending, bottoming, and coining allow for varying levels of precision and force application. Proper tool selection and material considerations, such as thickness and elasticity, are crucial to avoid defects like cracking or springback. Sheet metal bending is a cost-effective and efficient way to transform flat sheets into three-dimensional structures, making it a fundamental process in many manufacturing applications.
Why Choose Us For Sheet Metal Bending Parts?
- Precision & Expertise:
Our factory utilizes advanced CNC press brakes and experienced operators to ensure precise bending and consistent quality. We adhere to tight tolerances, delivering parts that meet your exact specifications every time. Wide Range of Capabilities:
We handle a variety of materials, including steel, aluminum, stainless steel, and more, with thicknesses ranging from thin gauges to heavy-duty plates. Our equipment and expertise allow us to tackle complex bends and intricate designs.Efficiency & Quick Turnaround:
With streamlined processes and state-of-the-art machinery, we deliver fast production times without compromising quality. Whether it’s a prototype or a large order, we ensure on-time delivery to keep your projects on track.Custom Solutions & End-to-End Service:
From design assistance to prototyping and final production, we provide tailored solutions to meet your unique needs. Our team works closely with you to optimize designs for manufacturability and ensure the best results.
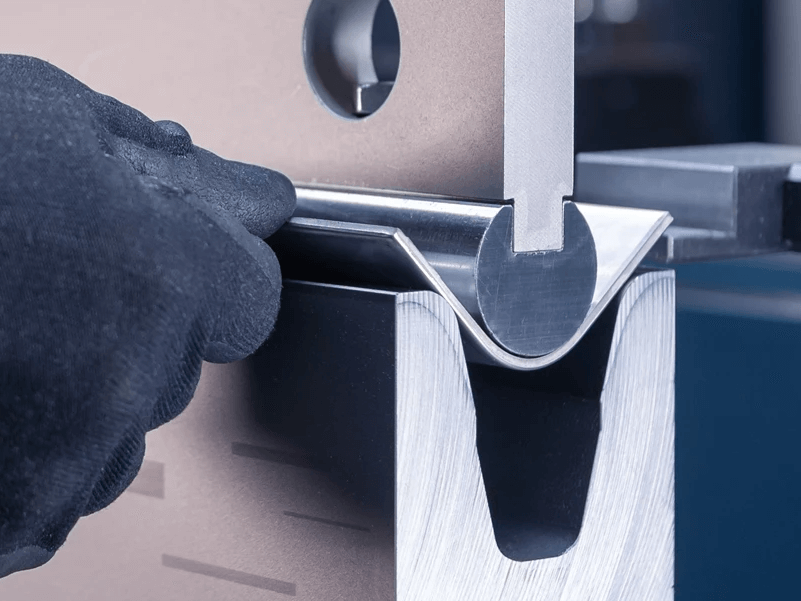
How does bending work?
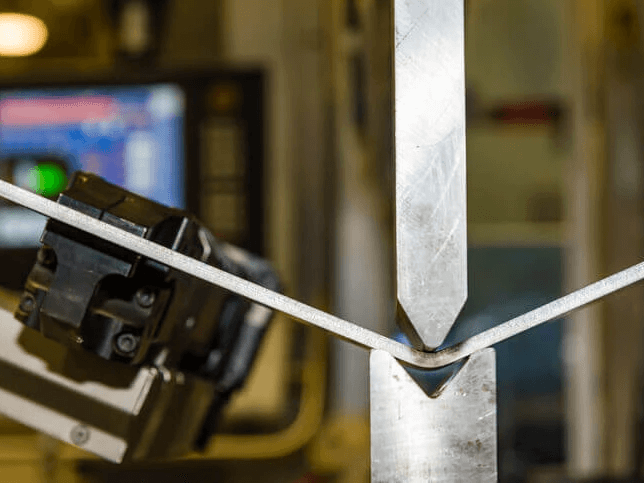
The bending and edging of sheet metal fall under non-cutting forming processes, where mechanical force is applied to shape the workpiece. The bend angle can vary widely, and the process is categorized into sheet metal bending and the round bending of bars and tubes.
There are three primary bending methods. In die bending, a punch forces the material into a die that has the desired final shape.
In swivel bending, the sheet is secured in a stop system, and an upper beam presses it against a specially contoured lower beam. A bending beam then creates the desired angle in the sheet.
In roll bending, sheets are fed through rotating rolls that form the material. Using profiled rollers, patterns can also be imprinted onto the sheet metal.
Sheet Metal Bending FAQs
What is sheet metal bending?
Bending is one of the most common sheet metal fabrication techniques. With bending, metal is deformed with specialist machinery into an angular shape. The bending of sheet metal allows a wide variety of part geometries to be produced and is particularly useful when performed alongside cutting. The most commonly used method for each process is CNC laser cutting and brake press bending.
What is sheet metal bending used for?
Sheet metal typically refers to the use of material under 3mm thick, but bending can be performed on materials far in excess of this, up to 8mm or more depending on material yield strength and the tonnage of the press being used. The process is very flexible regarding the range of materials and thicknesses that can be processed and the complexity of the parts that can be produced.
Bending is ideal for making a wide array of parts, used in every industry from automotive, transport, domestic appliances, furniture, industrial equipment and more.
What are some of the bending methods?
Die Bending: The material is pressed by a punch into a die that has the final desired shape.
Swivel Bending: The sheet is held in a stop system, where an upper beam presses it against a specially shaped lower beam, and a bending beam then forms the angle.
Roll Bending: Sheets are passed through rotating rolls that shape the material, and profiled rollers can even transfer patterns onto the sheet metal.
Which materials are suitable for bending?
Materials suitable for bending include ductile metals like mild steel, stainless steel, aluminum, copper, and brass, which can withstand stress without cracking. Thinner sheets and softer tempers bend more easily, while brittle materials may need special techniques to avoid failure.
What are the advantages of sheet metal bending?
Sheet metal bending offers precision, cost-effectiveness, and versatility, producing strong, complex parts with minimal waste. It works with various metals, supports rapid prototyping, and is efficient for both small and large-scale production.