Let’s look at the development of CNC technology. It goes from hardware NC, computer CNC to the current intelligent stage.
Hardware Numerical Control Machines (NC)
First generation: the era of electron tubes (around 1952)
In 1952, the Massachusetts Institute of Technology and Parsons Company together invented the world’s first three – axis CNC milling machine. Its control device is made up of over 2,000 electron tubes. The servo mechanism uses a hydraulic system. This marks the birth of CNC technology. The CNC system at this time has simple functions. It can only do basic point control and inputs instructions through punched paper tape.
Second generation: Transistor era (around 1959)
In 1959, CNC machine tools using transistors and printed circuit boards showed up. Machining centers with automatic tool changers also appeared. This brought CNC equipment into the second generation. There are some improvements in reliability and functionality.
Third generation: Small – scale integrated circuit era (around 1965)
In 1965, integrated circuits were used in CNC systems. This made CNC devices smaller, with lower power consumption and higher reliability. It helped the development of CNC machine tool varieties and output.
NC processing uses digital signals for control. It mainly achieves processing through preset programs. The control logic is quite fixed. The flexibility and programmability are low. Once the program is set, it’s hard to change the control parameters and logic during operation. At this stage, the processing accuracy is relatively low and the efficiency is low too. It can only do simple processing tasks, like ordinary turning, milling, drilling, etc. It’s suitable for processing parts with simple shapes and low precision requirements, like the rough processing of ordinary cnc mechanical parts.
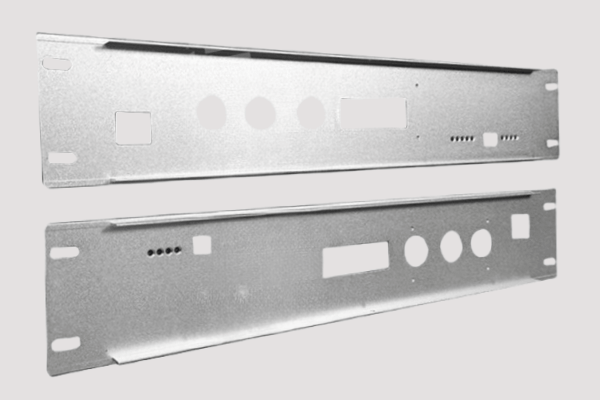
Computer Numerical Control Machines (CNC)
fourth generation: the era of small computers (around 1970)
In 1970, the CNC numerical control system made of small computers was shown for the first time at the Chicago Exhibition. The strong computing and control abilities of small computers let the numerical control system achieve more complex functions, like linear and circular interpolation. It can control multiple coordinate axes at the same time, improving the accuracy and efficiency of processing.
fifth generation: the era of microprocessors (around 1974)
In 1974, the United States, Japan and other countries developed CNC systems with microprocessors as the core one after another. It’s also called MNC. It uses the program in the computer memory to finish the functions needed for numerical control. It realizes decoding, tool compensation, speed processing, interpolation, position control, etc. through software. This cuts down hardware costs and improves reliability and flexibility.
The sixth generation: PC – based era (around 1990)
In the 1990s, with the fast development of personal computers, PC – based CNC systems came out. This system has the features of openness, low cost, high reliability, and rich software and hardware resources. Users can do secondary development and system integration according to their own needs. This makes the application of CNC systems more flexible and widespread.CNC manufacturing is controlled with computer technology as the core. It has high flexibility and programmability. Programs can be written or changed anytime through software according to machining needs. Machining parameters and control logic can be adjusted. At this stage, higher machining accuracy can be reached. The efficiency is greatly increased. It can do complex machining tasks. It’s widely used in aerospace, automobile manufacturing, precision instruments, mold manufacturing and other fields that need very high processing accuracy and efficiency. It can process complex curved surfaces and multi – axis linkage parts, like aircraft engine blades, automobile molds, etc.
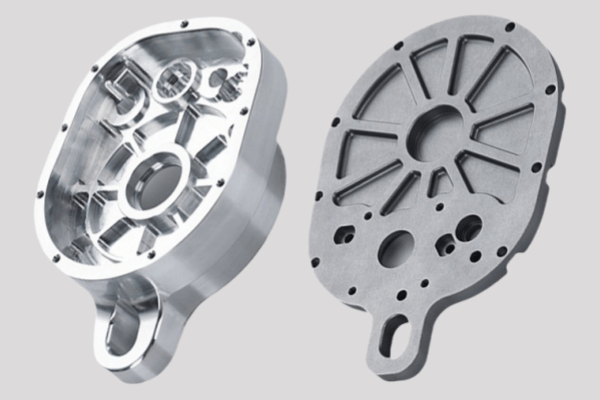
Modern intelligent and networking stage
Intelligent development
CNC systems have functions like adaptive control, fault diagnosis, and automatic optimization of processing parameters. For example, the system can adjust cutting parameters automatically according to real – time feedback during the processing, like tool wear and workpiece deformation. This improves processing quality and efficiency and reduces human interference.
Network development
Functions like remote monitoring, remote programming, remote diagnosis, etc. have been achieved. Operators can operate and monitor machine tools from far away through the network. Factories can manage and schedule multiple machine tools centrally, improving the production informationization level.
Higher technology development
There is multi – axis linkage and high – precision machining. For example, five – axis linkage or even more – axis linkage can process more complex spatial surfaces and part shapes. At the same time, by improving the accuracy and response speed of the servo system, optimizing the interpolation algorithm, etc., the machining accuracy is improved from the traditional millimeter level to the micron level or even the nanometer level.
Now, precision CNC machining is still developing and moving towards higher technology. Its aim is to use the least cost (shortest time, least labor) to make the best parts (higher accuracy, 100% good products).