Electrophoretic coating technology, as an important part of modern coating technology, has been widely used in the fields of automobiles, home appliances, etc. with its unique advantages. This article aims to summarize the basic knowledge and equipment characteristics of electrophoretic coating technology and optimize and polish the relevant content. So that readers can better understand and apply this technology.
Process
Electrophoretic coating is the process of using the electric field to make the charged paint particles precipitate on the surface of the coated object and form a uniform coating film. According to the different charges carried by the paint particles. We can divide it into anion electrophoresis and cationic electrophoresis. Since the discovery of the electrophoresis phenomenon, this technology has continued to develop. From the initial practical application of anion electrophoresis to the later practical application of cationic electrophoresis to the emergence of new-century electrophoresis and environmentally friendly electrophoresis. People have been continuously broadening and improving the application field and performance of electrophoretic coating technology.

Advantages
Electrophoretic coating technology has many advantages. First of all, it’s coating conditions are easy to control and manage. And can achieve uniform film thickness, high permeability, and inner plate rust prevention. Secondly, since it is a water-based paint, It has almost no fire, solvent hazards and other dangers, and has a small environmental load. In addition, the solids in the electrophoretic coating are coated separately. Which can avoid the occurrence of undesirable phenomena such as agglomeration, lack of paint, and flow marks. However, this also has some limitations, such as the coated object must be electrically conductive, it is difficult to change the paint and color, and it is necessary to pay attention to the mixing of impurities such as ions and oil.
The manufacturing process of electrophoretic coating involves multiple links. The main raw materials include resin, pigment, solvent, additives, etc. Resin is the main component of electrophoretic coating, which is charged and water-soluble through steps such as amination and acid neutralization. Pigments are used for color adjustment and provide functions such as rust prevention and weather resistance. Solvents and additives are used to adjust the performance and workability of the coating. During the manufacturing process, it is necessary to pay attention to controlling the proportion and mixing order of each component to ensure the quality and stability of the coating.
Equipment
The configuration of electrophoretic coating equipment is crucial to achieving high-quality coating effects. The diaphragm system is a key part of the equipment. It can effectively remove impurities in the coating and ensure the quality and stability of the coating. In addition, the pure water supply and conductivity control of the polar liquid tank are also important links to ensure the stability of the process. When engaging in practical applications, professionals in the field must take the initiative. They need to select the most suitable electrophoretic equipment model and precisely determine the parameter settings. This process demands a comprehensive and in-depth analysis of multiple factors.
When applying electrophoretic coating technology, operators must pay close attention to a series of crucial operating points and essential precautions. First and foremost, they need to make sure, through meticulous inspection and thorough cleaning procedures. The surface of the object intended for coating is impeccably clean, completely devoid of any oil stains, dirt particles, and other impurities.
This is of utmost importance because even the slightest trace of contaminants on the surface can significantly undermine the quality of the coating. Leading to issues such as uneven coating thickness, blistering, or peeling. Moreover, it can also severely affect the adhesion of the coating, reducing the overall durability and performance of the coated product. Thus failing to meet the required standards and usage expectations. Secondly, it is necessary to control the parameters such as the time and voltage of it to avoid too thick or too thin coating. In addition, the electrophoretic equipment should be regularly inspected and maintained to ensure its normal operation and extend its service life.
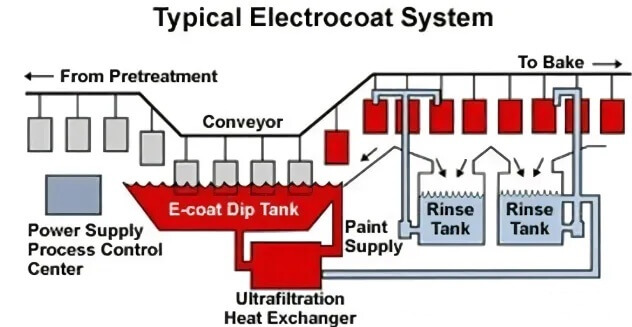
Summary
As an efficient and environmentally friendly coating process, The plays an increasingly important role in modern industry. By deeply understanding and mastering the basic knowledge and equipment characteristics of this technology. The continuously optimizing the operation methods and equipment configuration. We can better play the advantages of it, improve its quality and efficiency. It makes greater contributions to the development of the enterprise.
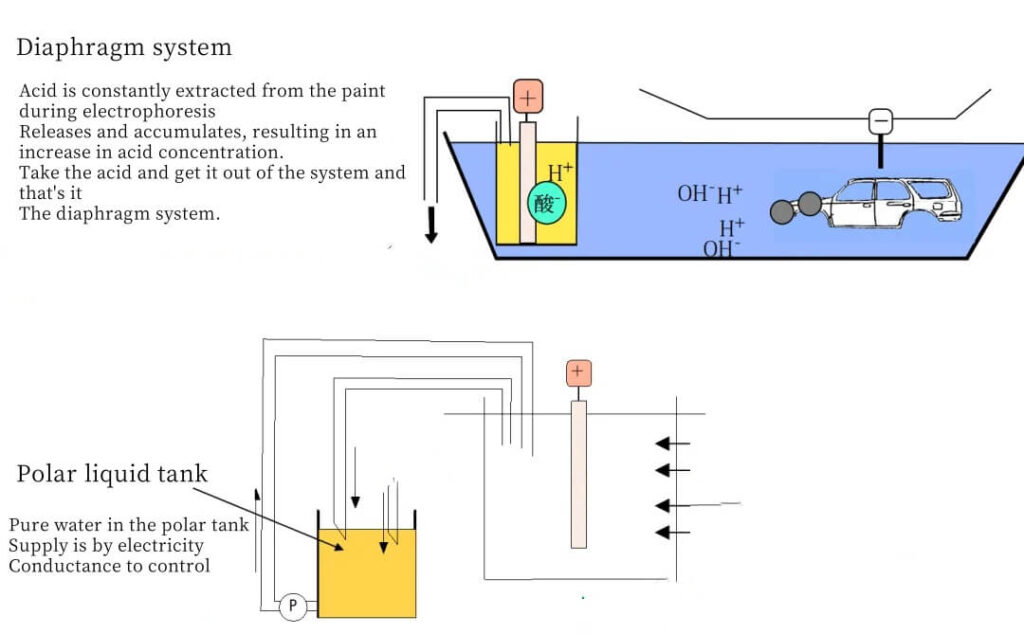