Electroplating
Electroplating is an electrochemical process that uses an electric current to deposit a thin, even layer of metal onto the surface of a substrate. This enhances properties such as corrosion resistance, wear resistance, electrical conductivity, or aesthetic appeal, depending on the metal used for plating.
What Is Electroplating?
Electroplating is an electrochemical process that deposits a thin layer of metal (like gold, silver, nickel, or zinc) onto a conductive surface. The object to be plated (cathode) is submerged in a solution containing dissolved metal ions (anode), and an electric current causes the ions to bond to the surface.
Purpose: Enhances corrosion resistance, improves appearance (e.g., shiny or decorative finishes), increases durability, and can add electrical conductivity.
Common Uses: Jewelry (gold/silver plating), automotive parts (chrome plating), electronics (copper/nickel plating), and rust protection (zinc plating).
Key Factors: Surface cleanliness, current density, electrolyte composition, and plating time affect quality. Poor control can lead to peeling, uneven coating, or defects.
How Does Electroplating Work?
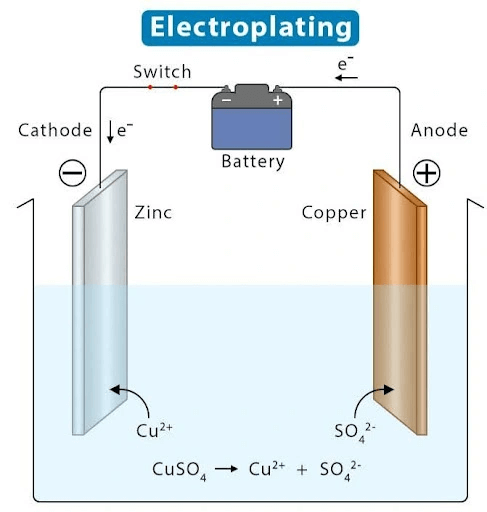
Electroplating uses an electric current to dissolve metal from an anode and deposit it onto a cathode (the workpiece). The process involves four key components:
Anode – The metal (or alloy) that will form the plating layer, connected to the positive (+) terminal.
Cathode – The workpiece being plated, connected to the negative (-) terminal.
Plating Solution – An electrolyte (e.g., CuSO₄ for copper plating) containing metal ions that migrate to the cathode.
Power Source – A DC supply that drives the metal ions from the anode to the cathode.
When current flows, metal dissolves from the anode, travels through the solution, and bonds to the cathode, creating a smooth, durable coating.
Advantages of Electroplating
Corrosion Resistance
Industrial components and outdoor products often face harsh environments. Plating with metals like chrome, nickel, or gold provides a protective barrier, preventing rust and degradation while maintaining long-term performance.
Enhanced Aesthetics
Electroplating gives surfaces a polished, high-end finish while masking minor imperfections. Gold delivers a luxurious luster, while chrome creates a sleek, reflective shine—ideal for decorative and functional applications.
Increased Wear Resistance
A layer of durable metals like nickel or chrome significantly boosts surface hardness, reducing wear and extending the lifespan of moving or high-contact parts.
Better Electrical Conductivity
For electronics and connectors, plating with highly conductive metals like copper or gold ensures optimal electrical performance and reliable signal transmission.
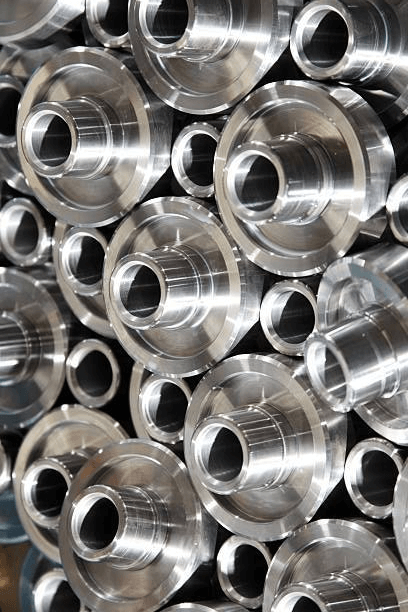
Electroplating FAQs
What is electroplating?
Electroplating is a process that uses an electric current to reduce dissolved metal ions onto a conductive surface, forming a thin, durable metal coating. It is commonly used for decoration, corrosion resistance, and improving conductivity.
When to Use Electroplating?
Electroplated coating is not only for aesthetic appeal and protection from external conditions but also has other uses. It can customize the surface properties by adding a layer of suitable metal through electrolysis. It can be used for these 5 conditions:
1. Dimensional Precision (Build thickness)
2. Aesthetic Requirements
3. Need for Corrosion Protection
4. Electrical Conductivity
5. Heat Resistance
How does electroplating work?
The object to be plated (cathode) is submerged in a solution containing metal ions (electrolyte).
A metal anode (source of plating material) is also submerged in the solution. When an electric current is applied, metal ions from the electrolyte are deposited onto the cathode.
What are some common applications of electroplating?
Automotive industry (chrome-plated bumpers, wheels)
Electronics (gold-plated connectors, PCBs)
Jewelry (gold and rhodium plating)
Aerospace (corrosion-resistant coatings)
Household items (silver-plated cutlery)
What is the difference between electroplating and electroless plating?
Electroplating requires an external power source to drive the deposition.
Electroless plating uses a chemical reaction (autocatalytic process) without electricity.