You can understand the difference between CNC 3 axis, 4 axis and 5 axis by reading this document.
Different processing methods
3 axis CNC processing: Usually, it means three axes with variable – speed linear motion in different directions, like left and right (X axis), up and down (Z axis), front and back (Y axis). The tool can move along three mutually – perpendicular coordinate axes relative to the workpiece. And it can only process one surface at a time.
4 axis CNC processing: Based on the three axes, a rotating axis (usually A axis or B axis) is added. Usually, the reference surface rotates 360°, but it can’t run at high speed. Through the linkage of four axes, usually three surfaces can be cut each time.
5 CNC processing: Based on the four axes, another rotating axis is added (usually an axis that rotates 360° on the vertical surface, like C axis, or another rotating axis like A axis and B axis, forming a 5linkage). This has achieved all – around processing. The five axes work together, allowing the tool to do complex spatial movements during the processing. And it can finish the processing of multiple surfaces in one clamping.
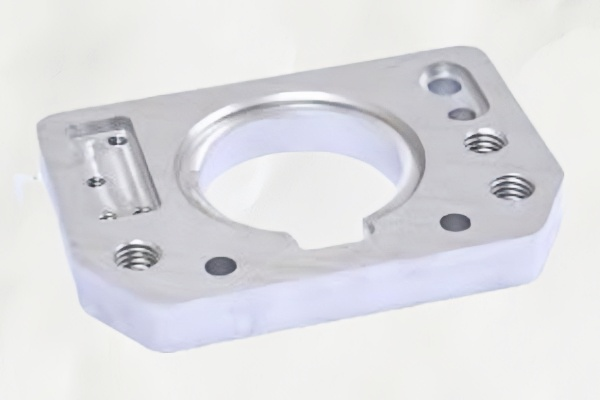
Processing Capability
3 axis CNC machining: The precision is low. It’s suitable for most normal milling, drilling and cutting operations, and also for machining flat parts and simple 3 dimensional cnc parts.
4 axis CNC machining: The precision is medium to high. It can do multi – faceted machining. It’s suitable for cnc machining complex parts with inclined surfaces or specific angle requirements, which are hard to do with 3 axis mill
5 CNC machining: The precision is high. It offers extremely high machining flexibility. It can deal with parts with complex geometries and high – precision requirements.
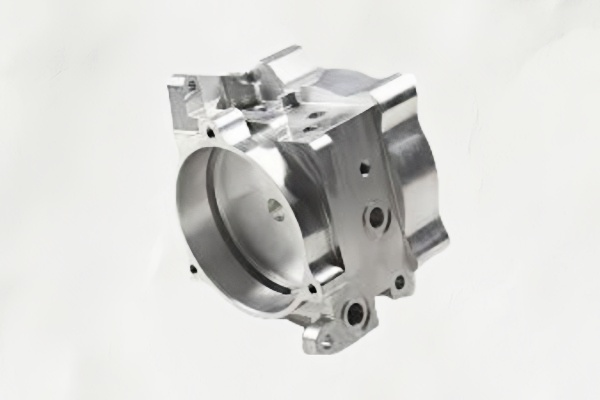
Advantages and Disadvantages
3 axis CNC machining
Advantages: The cost is low. It’s easy to operate. You can layout and design to process multiple parts at the same time. It has an advantage in mass – producing simple cnc parts.
Disadvantages: There are many clamping times. It can only do simple 3 dimensional machining. And it’s hard to process parts with complex geometries.
4 axis CNC machining
Advantages: Multi – faceted machining meets the complexity requirements. You can process multiple parts through layout design. It has an advantage in mass – producing complex parts.
Disadvantages: Buying a 4 axis machine tool is expensive. And the daily maintenance cost of the equipment is also high.
5CNC processing
Advantages: The degree of automation is high. It can finish part processing in one go. The precision and yield rate are the highest.
Disadvantages: The equipment cost is high. Programming and operation are complex. It can’t process multiple parts. It’s not suitable for large quantities.
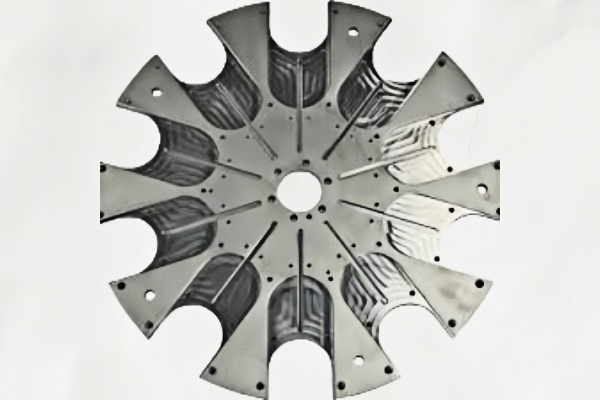
Most CNC factories have about 20% 3 axis, 60% 4 axis, and 20% 5 axis. 3 axis is used for simple part processing. 4 axis can be used for batch – producing complex parts. 5 axis can be used for sample production. It can finish the production of parts in one go, which is very suitable for customers who only need 1 – 2 samples.